

The Claus Sulfur Recovery Process
Sulfur recovery refers to the conversion of hydrogen sulfide (H2S) to elemental sulfur. Hydrogen sulfide is a by-product of processing natural gas and refining high-sulfur crude oils. There are many sulfur recovery technologies available for different applications, however the most common conversion method used is the Claus process. Approximately 90 to 95 percent of recovered sulfur is produced by the Claus process. The Claus process typically recovers 95 to 98 percent of the hydrogen sulfide feedstream. Only the Claus process will be described here, however please contact SRE for information related to any sulfur recovery process.
HYDROGEN SULFIDE (H2S)
SYNONYMS: SOUR GAS OR ACID GAS
‘Sour Gas’ is commonly present in natural gas and oil formations.
At low concentrations, it smells like rotten eggs
EXTREMELY dangerous as it is heavier than air, impairs our ability to smell/detect with increasing concentration, and exposure to >500 ppm can be fatal!
With respect to safety and product specifications, it must be removed from natural gas and petroleum products.
Thus, how do we safely rid ourselves of H2S and make another potentially valuable product?
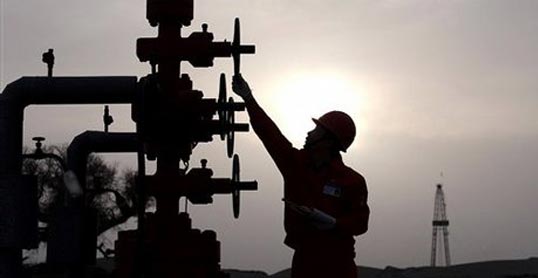

THE SULFUR RECOVERY UNIT (SRU)
The Sulfur Recovery Unit (SRU) is based on the modified Claus Process, which is a two-step reaction scheme overall. A portion of the total H2S is burned in the Reaction Furnace to form SO2. Then, the H2S and SO2 react, at an optimal 2:1 ratio, to form elemental Sulfur (Sx) across the Claus Reactors. After each catalytic stage, liquid sulfur is recovered in the Claus Condensers. The remaining unreacted H2S and SO2 then proceed to the next stage, where the equilibrium-limited Claus reaction continues in the presence of Claus catalyst.
MEETING SULFUR RECOVERY REQUIREMENTS
In general, gas processing plants and oil refineries are required to recover between 95 and 99.99 percent of the total sulfur introduced to the SRU. A conventional 2-stage SRU, with two Claus Reactors, is typically expected to recover 96+ percent. For a 3-stage SRU, the general expectation is 98+ percent. If necessary, a Tail Gas Cleanup Unit (TGCU) is required to recover the remainder.
Emissions regulations are only becoming more stringent each and every year! That’s where SRE can help out. Our specialized testing services ensure that the operation of your SRU is optimized for long-term performance and reliability purposes!

Access our technical webinars
The SRU Optimization series, which describes how to optimize the performance of each individual process unit, and covers 2 case studies from past testing experiences at SRE.
This is the final case study, where we’ll look at a testing job from about ten years ago at a refinery, and this is still a big client of ours to this day. So upon initial sampling we found that both feed streams had above threshold amounts of higher hydrocarbons (C2-C6), indicating over-circulation in the amine unit, and inadequate skimming operation of the SWS.
The low quality feed streams (& high contaminants) caused low thermal conversions.
High h/c content caused high CS2 formation. Poor hydrolysis, leading to 1.3% combined losses. And then their ADA signal was a little wonky from the inaccurate TGA readings. They were getting just under 96% recovery efficiency, with pretty much each stage underperforming.
SRE engineers then built a simulation model of the plant on that first night of testing and were able to provide some good guidance the following day. We increased the RF co-firing for better destruction temp, we increased the converter 1 temp, while reducing converter 3’s temp. And finally we lowered the final condenser temperature to 130°C. The increased RF temperature lowered the ammonia and BTEX breakthrough and jumped the thermal conversion efficiency to 50%. Increased the converter 1 hydrolysis by nearly 10%. But, with the increased co-firing rates came elevated gas mass velocities in the condensers, this increases the risk of liquid sulfur carryover to the next stages. Therefore, it was recommended that all the tubesheet blanks be removed to bring the velocities back down to normal. And, since the CS2 formation was still high, we recommended they review the circulation rates in the amine unit and the skimming operation of the SWS unit to attempt to reduce hydrocarbons and BTEX to the SRU.
So when we returned for the next set of quarterly testing, we found a much more accurate TGA, both feed streams were more optimized with less hydrocarbons, and the mass velocities dropped down into the normal range because they removed the tube blanks. This performance test, along with an incinerator optimization study, boosted the client’s recovery efficiency to well above the license, it improved the upstream unit’s operation, and the catalyst life was increased. This granted them huge savings in maintenance and fines, and greatly reduced their greenhouse gas emissions. It ended up being one of many examples of why testing and optimizing an SRU is often much more beneficial than some people might think.
And that brings us to the end of this webinar. Thank you for attending, and if you liked this presentation – consider looking into our on-site training, where we can send an engineer to your location to provide a wide range of courses regarding SRU’s and amine sweetening units. There is just one cost per course, not per person. So now I will take the time to answer any of your questions.
We will start this section by discussing the common issues associated with SRU feed streams. Since the SRU is only as good as what it receives, there are many potential areas for troubleshooting with regards to upsets with the feed stream units.
All SRUs have an Amine Acid Gas feed stream, and many refineries have an additional Sour Water Stripper Acid Gas feed stream. The first indication that there may be an issue with your feed streams is swings within your air demand signal. Large and uncontrollable swings in the combustion air demand signal occur due to fluctuations in the acid gas compositions and flow rates. Typically, when these fluctuate by more than 10%, the Air Demand Signal will fall outside of the optimal range and result in an immediate loss in recovery efficiency.
While plant swings can be unpredictable, they can be prepared for, new gas streams should be introduced slowly for a smoother transition. This can, for example, give the ADA time to adjust to the changing H2S content in the feed stream. Plant upsets can never be fully eliminated, so the SRU instrumentation must be regularly calibrated in order to be prepared for feed stream swings.
Full performance testing of the upstream amine and SWS units is the best way to optimize performance and minimize swings in the feed stream compositions and flows.
Another common issue with SRU feed streams is when they have high hydrocarbon contents. Hydrocarbons require much more oxygen to oxidize in the reaction furnace, which throws off the air demand. Also, more hydrocarbons means more CS2 production, which will hurt the recovery efficiency if it isn’t hydrolyzed. If sufficient amounts of hydrocarbon make it into the converters, catalyst poisoning will occur and deactivate the catalyst.
Excessive accumulation of HCs in the feed streams can be due to:
• Over circulation of amine, or amine temperatures falling below inlet gas temperatures, which results in HC condensation.
• Insufficient flash tank residence time or skimming operation can also increase hydrocarbons in the amine or sws acid gas. The same goes for the reflux drum.
• Sometimes the Reflux Drum purge rate is too low, or sometimes the pump does not start, resulting in LPG carryover to the RF.
The best way to minimize hydrocarbons in the feed streams is to perform regular maintenance, testing, and optimization of the amine and sour water units.
It is very important to maintain the SWS acid gas feed stream above 180F in order to keep this line from plugging. If the temperature is allowed to drop below this value then NH3 salts may begin to precipitate out and can eventually plug the line off entirely. The piping needs to be adequately heat traced and insulated all the way to the Reaction Furnace
The next common troubleshooting item we will discuss is high pressure drops in the SRU. Because SRUs operate at such low pressures, typically below 5 psi, it is not always easy to identify an abnormal drop in pressure across any given vessel. Trending the front-end pressure at the Reaction Furnace is often the best way to observe any abnormal pressures. In the worst case, the high pressure drop will limit the amount of feed gas that can be processed in the unit; thus, limiting the capacity of the train.
Pressure drops most commonly occur in converters and condensers, and they can be caused from the following:
• Sooting off the top of the first Converter while conducting a start-up or shutdown procedure (meaning a sub-stoichiometric natural gas burn has taken place).
• Amine carryover to the SRU can result in the fouling of the first Converter and cause a pressure drop.
• A flooded condenser due to plugged rundown lines/seal legs can cause small pressure drops in the SRU, but can go unnoticed (so its important to check rundown flows multiple times per day).
• Incomplete destruction of Ammonia in RF can result in the formation of ammonia salts, which can plug off condenser tubes.
• Incomplete combustion of acid gas feed stream contaminants can result in the formation of carbonaceous deposits, which will discolor the sulfur and deactivate and plug off the Converter.
• And finally, sulfur laydown is a common cause of pressure drops in SRU converters, and can be caused by operating at sub-dewpoint temperatures, or from liquid sulfur entrainment from the upstream condensers.
Troubleshooting SRU Burners (RF & Reheaters)
From there we will move onto some of the specific issues that can happen with the reaction furnace, starting with the instrumentation.
• Failures of the flame scanners is often due to the lens being coated with sulfur, soot, condensation, or corrosion products. All of this can be avoided with a properly set up purge system. If the purge systems do not have a rotameter for measuring flow then the purge air flow must be proven via another means. Flame scanners are a crucial safety element for the BMS. And also igniters are critical for safe start-ups and shutdowns, so there should be extras kept on-site.
• Fuel gas lines are not used often, so the system should be completely checked out before attempting any start-up or shutdown. Typical problems include plugged lines from moisture and corrosion. Having the fuel metered is highly recommended for safety and for historical records
• Failures in the optical pyrometers is normally due to the lens being coated, which can be rectified by ensuring that there is adequate flow of the purge air followed by a cleaning of the lens
• Ceramic encased thermowells must have a N2 purge to ensure that the corrosive gases from the RF do not penetrate the inner ceramic. This purge must be 3 to 5 psig higher than the pressure in the RF
• Proper air purges must be conducted before each attempt at a startup. If this is not performed, an explosion can occur within the RF- which can damage the main burner and checker wall
• Main Burner damage can be caused by burn-back due to low acid gas or fuel gas flow rates, corrosion, vibration, and plugging. All BMS logic should contain low flow shutdowns for both fuel and acid gas. Hydrocarbon carryover from the amine unit can cause fouling of the vanes and jets which can lead to plugging and vibration problems
• It is important that the Reaction Furnace rain shield is intact so that corrosion does not occur to the carbon steel shell
And this is what severe burner damage looks like, we can see that not only has the refractory lining eroded but also the burner shape itself has deformed. Operating the reaction furnace with a burner like this will create uneven mixing within the chamber and result in cold spots.
And that will bring us to reheaters
• Indirect steam reheaters can suffer from tube leaks, which can be indicated by unusual behavior with respect to process temperatures in the Reheater outlet and the corresponding Converter temperature profile.
• Liquid sulfur entrainment from the upstream Condenser can result in plugging and serious corrosion problems at or near the downstream reheater, this also causes a reduction in the Claus reaction in the converter.
• For Direct-fired reheaters, the burner management system, or BMS, must be reviewed regularly to ensure the proper burn stoichiometry is still being achieved, more specifically this means having the correct air to fuel gas ratio, or acid gas if it’s burning that. A burn ratio above 100 percent will result in excess air going to the converter, which can cause sulfation and risks a sulfur fire starting. Burn ratios that are too low, like below 70% in general, can result in soot deposition onto the catalyst. Our performance testing includes a DFR evaluation with downstream oxygen measurements to verify the correct burn stoich is being achieved.
• And then lastly, like any burner, having fully functional and calibrated instruments is key. We must know that the air and fuel gas flow rates are correct, and that the temperature indicator and control loop is functioning properly. Otherwise the BMS wont be working at its full potential, and we could have false converter inlet temperatures.
The SRU Troubleshooting series, which describes how to troubleshoot the common issues with each individual process unit, and covers 3 case studies from past testing experiences at SRE.
Now onto the wasteheat boiler and condensers, and seal legs.
• Thermal shocks to the WHB can result in a tubesheet leak so it is very important to make sure that the RF temperatures are controlled when warming up or cooling down. The recommended heating and cooling rate is 50°C per hour.
• Low levels in the WHB are particularly dangerous since exposed tubes are subject to extremely high temperatures from the Reaction Furnace, and it is therefore critical that the level column be reporting accurate boiler feed water levels
Condenser tubes can be fouled by Sulcrete, NH3 salts, or just solid Sulfur
• Like the WHB tube sheet failures are caused by thermal shock and corrosion
• Tubesheet failures can result in freezing/solidifying the sulfur which can plug off the rundowns and seal legs. A tube or tube sheet failure can be identified by steam coming from the lookbox or from seeing slug flows of the sulfur. In the worst case, the solid sulfur ‘bridging’ in the outlet end of the condenser completely plugs off and allows the condenser to flood entirely with liquid sulfur, which is then carried over to the downstream Reheater/Converter
• Failures in a Converter bed screening/grating can result in catalyst falling into the outlet nozzle of the Converter and into the Condenser, finally ending up in the bottom of the seal leg. Depending on the amount of catalyst that has migrated into the seal legs, the legs can be either pulled and cleaned or isolated, then 50 psig steam or compressed air can be used to blow the catalyst out of the seal leg.
• Rodding the rundowns, seal legs, and up into the outlet section of the Condenser may allow for continued operations until the train can be brought down for repairs
The most important factor in designing sulfur condensers is the mass velocity of the process stream. If velocities are too low, sulfur fogging can occur, if velocities are too high, sulfur re-entrainment can occur, both leading to sulfur carryover, and a reduced recovery. Liquid sulfur entrainment is especially detrimental when it occurs in the final condenser, where losses can be upwards of 1.5% off the recovery efficiency.
Capacity evaluations by way of VMG simulation software can determine the optimal mass velocity through the condenser process tubes. These capacity evals should be up to date with the process parameters and are essential when operating at a high turndown, or expecting to in the future.
Here are some pictures of the common condenser problems, in the top left we see condenser tubesheet that’s been pulled and water tested, all the water coming out of the tubes would suggest that it failed this leak test miserably. The top right picture is what sulfur concrete, or ‘sulcrete’ looks like in a rundown, and sulcrete can be formed when there are impurities in the liquid sulfur such as catalyst dust or hydrocarbon soot. And we will typically see a buildup of sulcrete when the rundowns haven’t been cleaned before a start-up and there's still dust and contaminants in there. The bottom left picture is a hole in a multi-pass condenser and we’ll actually cover a case study about that later on. Then the bottom right picture is of sulfur that has built up and partially plugged the outlet of a condenser which could have been due to long continuous sulfur entrainment, or from a tubesheet leak.
The SRU Troubleshooting series, which describes how to troubleshoot the common issues with each individual process unit, and covers 3 case studies from past testing experiences at SRE
Converters, where the catalytic reaction takes place.
• If the temperature rise across a converter is observed to be lessening, this indicates that deactivation is occurring. This phenomena may be accompanied by an increase in the temperature rise in the downstream Converter since it now has to do ‘more work’. We also need to be aware of an increase in the RF pressure, which may indicate that one of the Converters has gone ‘sub-dewpoint’ and is plugging off due to liquid sulfur.
There are a number of mechanisms that can cause catalyst deactivation. They include BTEX and methanol poisoning; sulfation; carbon fouling, hydrothermal ageing; and normal ageing.
BTEX poisoning occurs when the RF is unable to completely destroy BTEX components in the acid gas feed stream(s) to the SRU. The resulting effect is a ‘cracking’ or ‘polymerizing’ of these components on the Claus catalyst.
Methanol poisoning is normally due to an SRU with an acid gas by-pass that allows methanol to by-pass the RF.
Both of these poisoning mechanisms are permanent.
Soot deposition and liquid sulfur deposition on the top of the catalyst, results in plugging of the converter beds, but these can be reversible with a heat soak.
Sulfation of catalyst occurs when excessive free oxygen is carried over from either the RF or direct-fired reheaters;
Hydrothermal ageing results when the catalyst is exposed to excessive amounts of water vapor over a long period of time. Although the actual physical mechanism is still not completely understood, it can occur when either excessive steam is introduced into the process and may also occur due to serious tube or tubesheet leaks (BFW being on the shell side) from the Wasteheat boiler or Condensers.
Thermal ageing is caused by ‘thermal excursions’ or ‘sulfur fires’ in the catalyst beds. Temperatures above 1300 F, which are all too easy to obtain during a serious sulfur fire, can result in ‘fusing’ of the catalyst into large solid pieces.
And then more quick notes;
• Exposure to large amounts of condensed water will result in immediate destruction of the catalyst pellets.
• And If there is a sudden step-change reduction in the temperature rise across the first Converter, this would indicate that a severe carryover of contaminants such as hydrocarbons and/or amine has occurred
• A sudden increase in temperature in the Converters will be due to a ‘sulfur fire’. This means that there is free oxygen getting to the Converters either from the RF and/or the Reheaters. If the problem is not corrected quickly, it will be necessary to introduce ‘snuffing steam’ or an inert gas to stop the fire. Do not allow the temperatures to go above 450C in the Converters or there will be severe damage done to the internals.
• Damage in the Converter internals normally shows up as a failure in the catalyst supporting mesh screen and grating, which will result in catalyst falling through and ending up in the Condensers, Rundowns, and Seal Legs (often plugging is the result). In the worst case scenario the carbon steel support beams will bow downward or collapse.
So to quickly sum up the troubleshooting process for catalyst deactivation, once the specific mechanism has been identified, we need to eliminate the cause, whether it be air, soot, or poison going onto the catalyst, or if its just normal aging that we need to minimize with smoother start-up and shutdowns. Once the cause has been taken care of, we need to assess the performance of the converter, is the temperature profile still ok, is the conversion reasonable? Then we can take the necessary planning steps to either do a heat soak to try a reversible, if applicable. Or to plan a catalyst changeout for the next shutdown.
The SRU Troubleshooting series, which describes how to troubleshoot the common issues with each individual process unit, and covers 3 case studies from past testing experiences at SRE.
So now onto the sulfur pits, or degassing pits. The two key elements for degassing are agitation and gas sweeping, where the agitation can be from continuous circulation, from dropping through tray columns, or from an actual agitator which shakes the liquid sulfur. These processes break the H2S out of solution, so then the gas sweeping aspect can move the H2S out of the pits and to the incinerator. Some degassing pits also use a chemical catalyst to improve the process of breaking the H2S out of solution.
So when the degassing becomes less effective and too much H2S is remaining in the sulfur, it could be due to a number of issues in the process. Sometimes the agitation equipment malfunctions, like a broken pump or agitator. And sometimes the air blowers will stop working. The reason for poor degassing can be difficult to identify so often times professional sampling of the liquid sulfur must be done. This process would include sampling each different stage of the degassing process as well as the sulfur pit inlets and outlets. By sampling incrementally and moving upstream, we can quickly identify the problem area and take action to bring the sulfur product back up to spec.
And that brings us to our next case study, which is about the sulfur pits. Last summer we were brought in to a gas plant to investigate increasingly severe glycol losses from an unknown location in the SRU. This plant has 3 SRU trains, with a common MCRC tail gas unit. All 3 condensers used glycol, and all the rundowns and the lines to the pit were heated with glycol, so there were quite a few locations to look for a possible leak.
With a 60:40 glycol to water mixing ratio, the amount of total diluted glycol lost was estimated to be over 1,500 L/day. So we had to quickly come up with method to test for the source of the leak without having to add any tracers to the process, which may impact the quality of the sulfur product.
SRE devised a plan to sample from the pit outlets first, then move backwards (or upstream) until the exact source of the glycol was found. We first tested the pit outlet lines and found glycol in 2 of those 3 outlets. Next we tested each stage within those 2 pits, and we found that the entire #1 pit had glycol contamination, but only the last 2 sections of the #2 Pit. So this led us to conclude that there had to be a leak somewhere between the first and second sections of Pit 2. Then we had to check all the Condenser rundowns that led to Pit #1 to find that leak, which ended up being in the second Condenser’s tubesheet, and was found to be much more severe of a leak. Now that the leaks were identified, they could be repaired during a fairly quick shutdown.
So our team stayed on site to assist with a smooth shutdown of those 2 trains, and we were even able to see how bad the condenser leak really was. That, and the pit tracing leak were patched up, and the SRU was started back up 24 hours later.
In conclusion, both leaks were identified and then repaired in a timely manner. We didn’t have to use tracers, and we analyzed all those liquid sulfur samples on site, with fast results. And we saved them a bunch of money by stopping the glycol losses, and cleaning up the sulfur product back to normal.
The SRU Troubleshooting series, which describes how to troubleshoot the common issues with each individual process unit, and covers 3 case studies from past testing experiences at SRE.
So now well move onto the Thermal Incinerator, and well start by reviewing some of the possible reasons for seeing an increase of emissions at the Continuous Stack Emissions Monitor (CSEM) which is typically located on the incinerator stack. So increased emissions could be due to:
• An upset in the Claus plant, which results in off-ratio conditions and a reduced overall sulfur recovery
• It could be from Liquid sulfur entrainment in the final Condenser, or from
• Flooding of the final Condenser due to plugged off rundowns or seal legs, which could be from a tube sheet leak, or sulcrete forming in the rundowns, or just sulfur solidifying there.
• Also Deactivation in one or more of the Converters will obviously increase emissions
• Damage or failure of the Reaction Furnace’s main burner would lower the thermal conversion and increase emissions
• And then a sulfur fire in a piece of equipment or a vessel will also create more emissions
And now we’ll talk about common issues that happen with the incinerator itself.
The first is operating with an incorrect burn stoichiometry, which typically leads to too much excess oxygen in the stack. If there is 2 to 4 percent O2 then the stoich is good, but often times the O2 analyzer is unreliable due to the acidic nature of the stack gas, and more specifically the sulfuric acid formation taking place. These analyzers need to calibrated and maintained often, just like all instrumentation. When the O2 levels are too high then that means fuel gas usage is likely too high as well, and the more FG burned, then the more CO2 will be produced. This is why knowing the normal flow rates and temperatures in the stack is key, we must recognize when these conditions are deviating from the optimal levels.
The next common issue with the incinerator is operating at an elevated temperature, which is often associated with the excessive oxygen condition. But it can also be due to design flaws or the need for an updated operating design (or BMS). The threshold temperature in the stack is 650C. SRE performs Stack Top Temperature Reduction studies to determine the minimum allowable temperature that will still minimize the Total Reduced Sulfur. Operating at higher than optimal temperatures can also be caused by inaccurate thermocouple readings, or inaccurate flow measurements of the fuel gas or oxygen. Then lastly, when the Claus plant is performing poorly, then more TRS will be sent to the incinerator. And this can make it difficult for the BMS to maintain the correct stoich and temperature. So similar to the streams feeding the Reaction furnace, the Incinerator is only as good as what it receives in terms of Claus tail gas.
Historically, tail gas analyzer sample lines have been the cause of the bulk of this instrument’s operating failure. The simple reason is that the sample loop needs to be extremely well heated to ensure that the line does not plug with liquid or solid sulfur. The preferred method to use here is electrical heat tracing as it is easily controlled and it’s not affected by process upsets or steam trap failures. The critical area is where the sampling system connects to the process piping, since electrically heated valves are not practical, steam tracing is used at this connecting juncture. This is also why is it highly recommended to have a sample probe here that goes right into the process tail gas stream.
The second most common problem for tail gas analyzers is the loss of sample line flow. This may be due to a failure in the aspiration system or the possibly excessive liquid sulfur in the tail gas line due to liquid sulfur entrainment from the final condenser.
A reduction in the sample line flow rate will increase the lag time of the feedback signal to the trim air controller and can be detected by long and ‘looping’ air demand signal trends on the DCS. Keep in mind that sample lines should be as short as possible to minimize the response time of the sampling system.
By far the most common method for metering the acid gas feed streams and main/trim air flow rate is with orifice meters. These meters are accurate if they are set up properly and have a wide range for flow, which can be particularly useful during startups and shutdowns
The SRU Troubleshooting series, which describes how to troubleshoot the common issues with each individual process unit, and covers 3 case studies from past testing experiences at SRE.
So now we will move on to our next case study which is troubleshooting a low recovery efficiency. This was an existing client whom SRE visited several times in the past, they brought us in to troubleshoot their recently unexplained decrease in recovery efficiency.
Upon initial compositional analysis of the process gas, SRE found that the conversion across Converter 2 was low, other than that the SRU was being operated well and nothing else had changed since the previous test period. But the prilling station downstream of the SRU was also reporting high H2S levels in the product, suggesting poor degassing operation, but well get to that on the next slide.
Then the simulation was completed which reconfirmed the reduced activity observed in the second converter bed. The sudden reduction here made no sense, as the catalyst was just replaced 6 months prior, and virtually nothing else had changed which might deactivate the catalyst. Upon further analysis SRE discovered that the converter inlet temperature was above the normal recommendation, so we then installed a sample probe at the inlet of converter 2 and tested there. This analysis revealed a different composition here than at the Converter 1 outlet, when they should have been identical. This analysis, combined with much troubleshooting experience, led SRE to conclude that there must be hole in the multi-pass condenser, which was allowing some process gas from the first pass to leak through into the second pass, and therefore contaminating the Converter 2 inlet stream with RF outlet gas. This would fully explain the reduced conversion across that converter, as well as the increased inlet temperature to it. Now the degassing operation just needed reviewing.
Before the client shut down to repair the condenser leak, SRE wanted to evaluate the degassing pits to determine why 200 ppm of H2S was still in the liquid sulfur product. So we got the operator to make incremental adjustments, first to the agitator, then to the circulation rates from the pumps, and we sampled after each adjustment to observe the effect it would have on the H2S levels. We quickly found that the circulation rate was too low for adequate degassing and that it could not really be increased, it was then discovered that one of the two sulfur pumps was barely moving any sulfur and needed repairs. A pump repair was then planned, along with the condenser repair during the shutdown of the SRU. SRE assisted with the shutdown and then returned to site once the maintenance was completed, we assisted with a smooth start-up, and then performed another test to verify the results of the repairs. The overall recovery efficiency jumped back up above the license of 98%, and the liquid sulfur was back to the normal H2S content of about 50 ppm.
And here is a picture of that hole in the multi-pass condenser, and also a picture of some sulfur pumps on top of the degassing pit. To reiterate the conclusion of this case study, once SRE tested the SRU and degassing pits, the troubleshooting process was quick and prevented any further damage to the SRU, and prevented a sizeable amount of contaminated product from going to the prilling station. So it always pays off to catch the problem early and repair it before things get worse, and many of these SRU issues can only be identified with formal testing to see whats going on under the hood.
And that brings us to the end of this webinar. Thank you for attending, and if you liked this presentation – consider looking into our on-site training, where we can send an engineer to your location to provide a wide range of courses regarding SRU’s and amine sweetening units. There is just one cost per course, not per person.
This video is the full recording of the SRU Cost Savings Webinar from July 14, 2016. The video describes the costs that are associated with the SRU, and methods for reducing them. It also covers 3 case studies from past testing experiences at SRE.
1) Introduction
2) About SRE (2:46)
3) SRU Associated Costs (5:57)
4) Methods of Cost Savings (16:45)
5) Payback Period Examples (30:18)
6) Wrap-up (40:56)
7) Q&A (42:03)
Is plugging getting you down? Did you have a hiccup during your last SRU start-up?
This is the full recording of SRE's Sulfur Wash Webinar
Is plugging getting you down? Did you have a hiccup during your last SRU start-up? SRE has routinely helped our clients through this simple and effective method, avoiding the need of a costly emergency SRU shutdown and a catalyst skimming operation.
This video teaches how to identify the key indicators of a problem and the steps involved in performing a successful sulfur wash. Data compiled from a recent sulfur wash operation is presented.
1) Introduction
2) What is a sulfur wash? (6:07)
3) Identifying the problem (7:11)
4) Steps of a sulfur wash (21:22)
5) Recommended follow-up (31:21)
6) Wrap-up (35:54)
7) Question & Answer (38:35)
This video explains the process, and the benefits, of performing a complete Incinerator Optimization Study with Sulfur Recovery Engineering (SRE).
This is the condensed video recording of the Stack Optimization Webinar conducted in October 2016. This video explains the process, and the benefits, of performing a complete Incinerator Optimization Study with Sulfur Recovery Engineering (SRE).
Introductions (00:40)
Functions of Incinerator (4:34)
Why Optimize the Incinerator? (7:18)
Process Steps (12:21)
Case Study (21:36)
Wrap-up / Q&A (27:18)
Sulfur seals and rundown systems are the final components in the safe and reliable collection of the produced liquid sulfur product. Understanding this process equipment is essential for consistent operation, as well as troubleshooting the potential issues.
This webinar explains the different types of sulfur rundown systems, common problems associated with them, and optimization techniques for both above-ground sulfur seals and below-ground seal legs.Items discussed:
1. The purpose and function of sulfur seals and rundown systems
2. Troubleshooting the common problems associated with sulfur seals
3. Comparison of above-ground sulfur seals and below-ground seal legs
4. Optimizing sulfur seals and rundown systems
5. Question & answer period
This video covers fundamentals of Claus process, focusing on process chemistry, design principles, and typical configurations. We'll discuss how to optimize conversion and recovery efficiency, manage key operating parameters like the H2S ratio, and implement best operating practices.
This video covers fundamentals of Claus process, focusing on process chemistry, design principles, and typical configurations. We'll discuss how to optimize conversion and recovery efficiency, manage key operating parameters like the H2S ratio, and implement best operating practices.
Book a 1-1 Meeting with SRE